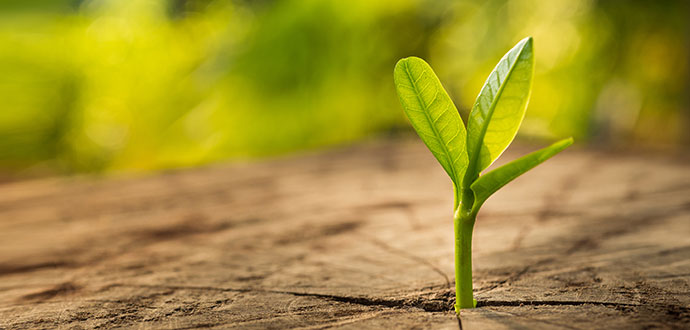
Environmental Protection and Occupational Safety
Occupational Health & Safety
In addition to complying with local labor laws and safety regulations, all major facilities have established and certified ISO 45001 Occupational Safety and Health Management Systems, encompassing employees and non-employee workers (coverage rate:100%). USI has a health and safety policy, standard operating procedures, educational training, and LOHAS activities to ensure workers' physical and mental health during working hours.
USI's seven major manufacturing facilities have set up Safety and Health Production Committees required by local regulations. According to the regulations, labor representatives should take up at least a third of the committee. The frequency of the committee meetings varies from facility to facility, but regular meetings are held at least quarterly to coordinate and recommend occupational safety and health management matters. To ensure the safety and health of workers in the facility, USI invested CNY 197 million in safety production and chemical safety management in 2023. Occupational safety and health costs include employee insurance, physical check-up, labor protection, safety measures improvements, operating environment monitoring, and ISO 45001 certification fee.
Safety and Health Production Committee's Responsibilities:
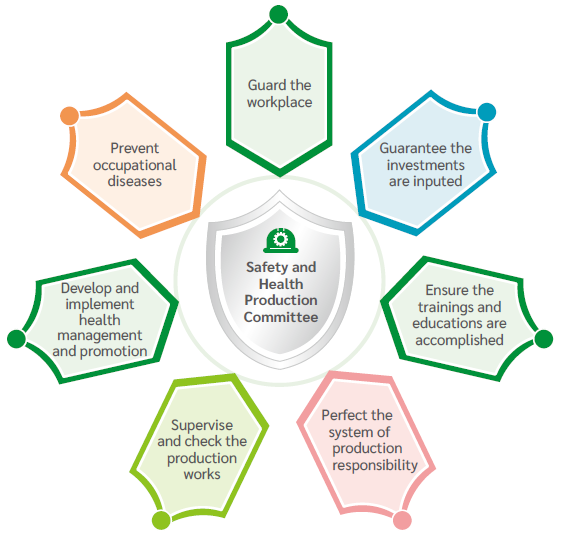
As part of the risk-based thinking required by the ISO 45001 Occupational Safety and Health Management System, USI establishes a process to manage procurement, contracts, and changes. We implement necessary safety assessments, trainings, and data updates to reduce potential safety and health risks from operating conditions or the work environment. To effectively identify and assess safety and health hazards and risks and opportunities derived from the operations and work environment, we request responsible units to identify hazards based on occurrence probability, exposure frequency, and consequence severity regularly each year.
Hazards, Risks, and Opportunities Identification Procedure:
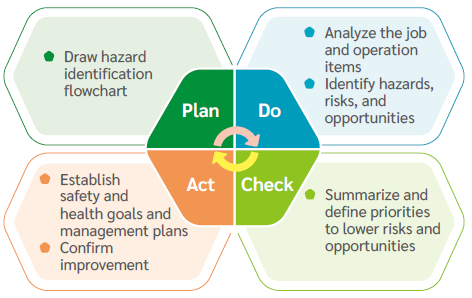
Hazards, Risks, and Opportunities Identification Management Measures:
Risk and Opportunity Level | Corrective Action | Identification Result | Hazard or Impact Above Medium Level | Management Measures |
---|---|---|---|---|
1. Serious | 1. Control measures must reduce the risk to an acceptable range 2. Review the integrity of existing protection and control measures and formulate plans for improvement. If there is no improvement, it is necessary to formulate operation control procedures or emergency response plans |
There are no Serious or High-Level risks in the work activities or working environment of USI facilities. | ||
2. High | ||||
3. Medium-High | It must be reviewed whether there are still opportunities to improve the performance of occupational safety and health, such as: 1. Measures to further reduce personnel exposure frequency or incident rate 2. Adjust the work, work plan, and working environment suitable for workers 3. Reduce the monotonous work or working frequency 4. Strengthen existing control measures |
Part of the factory operations and high-risk operations employees have Medium-High or Medium Level risks and opportunities; others are Low or Slight Level risks and opportunities. | Elevated operations: drop, fall | Must wear safety belts and helmets and use compliant auxiliary equipment; set up the operation control area and have workers from the same industry to assist in the operation. |
Confined space operations:hypoxia | Wear self-contained breathing apparatus and strengthen training. | |||
4. Medium | COVID-19: public health | Carry out relevant requirements and measures for personnel access control, self-monitor temperature, notification system, and environmental protection. | ||
5. Low | Hot work operation: fire | Must control fire sources and combustibles, wear personal protective equipment, carry spare fire extinguishers, and strengthen training. | ||
6. Slight | Work environment (such as using organic solvents, X-Ray inspections): inhalation hazard, skin contact hazard or body pathology | In addition to regular monitoring of high-risk operating environments (including lighting), environmental inspections should be conducted. The inspection items include noise, carbon dioxide concentration, organic solvents, specialized substances, dust, lead workplaces, and free radiation; they require personal protective gear during operation. |
To ensure the safety of workers and facilities, each facility conducts inspections in accordance with local government regulations and the Company's operating standards, and EHS personnel also conduct routine facility safety audits, with the scope encompassing Occupational Health and Safety Management Systems. In some facilities, the inspection results are included in the occupational safety and health evaluation activities, and outstanding units are publicly recognized in the regular occupational safety and health (production) meetings to encourage personnel to participate in safety and health management and improvement measures.
Audit Findings Results Over the Years:
Aspects / Year | 2020 | 2021 | 2022 | 2023 |
---|---|---|---|---|
Safety | 376 | 747 | 535 | 594 |
Health | 108 | 121 | 59 | 33 |
Management System | 11 | 47 | 13 | 0 |
In addition, according to the actual operating hazards of each facility, qualified institutions are also commissioned to regularly implement environmental testing to control the operating environment of the hazard factors, testing items such as building security, drinking water safety, sewage testing, Legionella pneumophila bacteria, emergency lighting, lightning protection testing, smoke detection equipment and fire equipment testing. At the same time, the company also regularly monitors operational environments with high risks including noises, the concentration of carbon dioxide, organic solvents, specific chemical substances, lead in the workplace and free radiation to ensure that the threshold values of concentration of harmful substances and noises are below standards. If there are any abnormalities, it will be immediately corrected and maintained; if it is close to the abnormal state, we will provide employees with appropriate preventive training, and with a healthy and safe working environment.
Occupational Health and Safety Training
In order to enhance employees' awareness of occupational safety and health, USI has established "Environmental Safety and Health and Energy Education and Training Management Regulations" at each facility to draw up annual environmental safety and health education and training plans according to practical needs, and to conduct safety and health education and training for new recruits and in-service personnel (e.g., chemical safety operation, electrical safety, personal protective equipment use and workplace accident management training), regulatory and certification training (e.g., first-aid personnel, special machinery and equipment safety management and radiation device operation training), management system operational training, emergency response training, and contractor training (please refer to the Contractor Management section), as well as arranging drills and tests for employees to enhance their knowledge and skills and their ability to deal with emergencies.
Occupational Health and Safety Training Data:
Items / Year | 2020 | 2021 | 2022 | 2023 |
---|---|---|---|---|
Total Number of Courses | 207 | 410 | 118 | 224 |
Total Number of Trainees | 56,285 | 50,851 | 10,967 | 19,956 |
Total Training Hours | 48,411 | 57,776 | 11,008 | 22,702 |
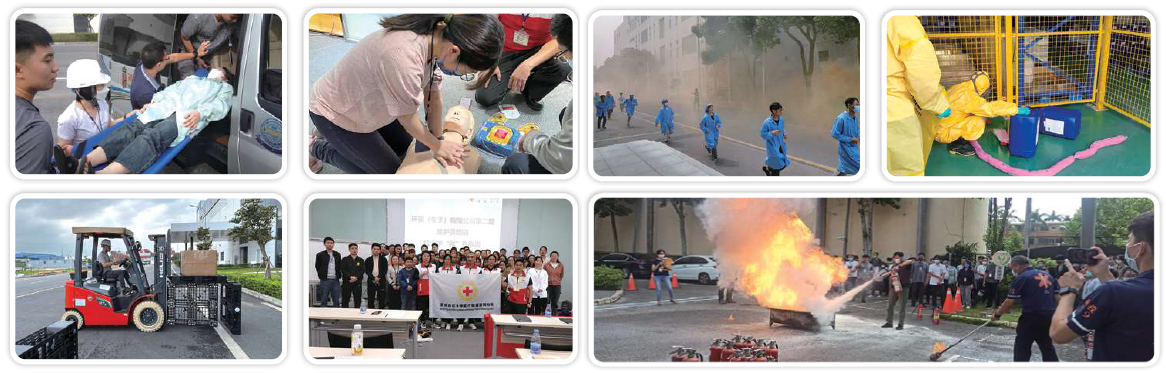
To ensure that the relevant units can respond quickly when an occupational incident occurs, each facility has established procedures for accident investigation and handling, stipulating that if a near miss, occupational injury or occupational disease occurs in the facility, procedures such as first aid, reporting, investigation, and improvement measures would be carried out, and at the same time improvement measures are proposed based on the root cause of the accident. All improvement measures would be carried out across all facilities, and relevant continuous improvement would be tracked regularly to prevent the recurrence of similar accidents. In 2023, there were 14 work-related physical injuries. In addition to improving the hardware and equipment, the company is also actively raising the safety awareness of its employees and continuing to work towards the goal of "zero accidents". There were no accidents resulting in injury or death of employees or damage to equipment resulting in production stoppage in 2023.
Occupational Injuries and Occupational Diseases:
Items / Year | 2020 | 2021 | 2022 | 2023 | |
Employee | |||||
Number of lost-time injuries | 12 | 14 | 11 | 14 | |
Lost-Time Injury Frequency Rate (LTIFR) | 0.29 | 0.31 | 0.23 | 0.37 | |
Number of high-consequence work-related injuries | 0 | 0 | 1 | 0 | |
Rate of high-consequence work-related injuries | 0 | 0 | 0.02 | 0 | |
Number of near misses | 0 | 2 | 5 | 0 | |
Near Miss Frequency Rate (NMFR) | 0 | 0.05 | 0.11 | 0 | |
Number of work-related fatalities | 0 | 0 | 0 | 0 | |
Rate of fatalities as a result of work-related injuries | 0 | 0 | 0 | 0 | |
Occupational Diseases Rate (ODR) | 0 | 0 | 0 | 0 | |
Number of days lost due to injuries | 124 | 460 | 309 | 444 | |
Lost Day Rate (LDR) | 2.95 | 10.33 | 6.54 | 11.74 | |
Contractor | |||||
Number of lost-time injuries | 1 | 0 | 0 | 0 | |
Lost-Time Injury Frequency Rate (LTIFR) | 0.27 | 0.00 | 0.00 | 0.00 | |
Number of high-consequence work-related injuries | 0 | 0 | 0 | 0 | |
Rate of high-consequence work-related injuries | 0.00 | 0.00 | 0.00 | 0.00 | |
Number of near misses | 0 | 0 | 0 | 0 | |
Near Miss Frequency Rate (NMFR) | 0.00 | 0.00 | 0.00 | 0.00 | |
Number of work-related fatalities | 0 | 0 | 0 | 0 | |
Rate of fatalities as a result of work-related injuries | 0.00 | 0.00 | 0.00 | 0.00 | |
Occupational Diseases Rate (ODR) | 0.00 | 0.00 | 0.00 | 0.00 | |
Number of days lost due to injuries | 24 | 0 | 0 | 0 | |
Lost Day Rate (LDR) | 6.37 | 0.00 | 0.00 | 0.00 |
Nowadays, outsourcing technical and professional projects to contractors are part of daily operations. Besides requesting contract project quality and schedule, USI values contractors' safety and health. USI's Policy clearly commits to "Awareness Training" and communication for all workers, and our Contractor and On-Site Construction Management Regulations were formulated using the concept and principle of the PDCA cycle, and we use the Regulations as our guidance to effectively manage and improve contractor occupational safety and health.
Contractor and On-Site Construction Management Regulations:
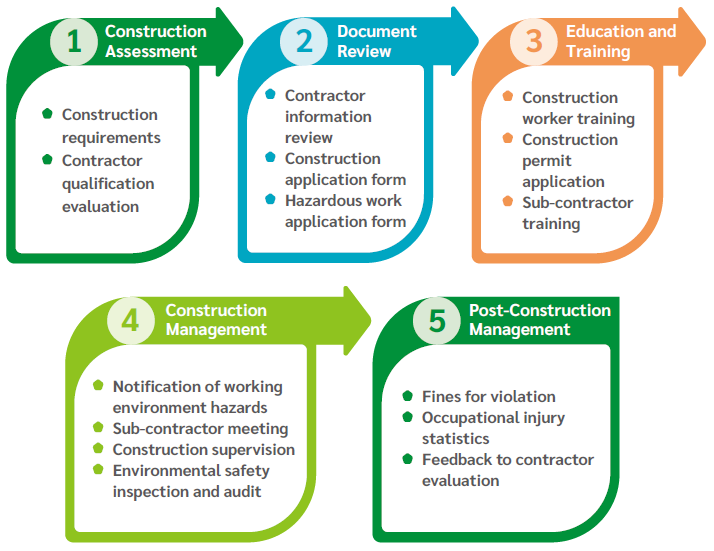
The quality of the contractor's personnel has a significant impact on the quality, duration, and safety of the work being contracted. Therefore, USI contractors are asked to provide the necessary documentation of education and training, as well as participate in occupational safety and health education and training conducted by USI. In 2023, more than 250 occupational safety and health training sessions were held for 2,300 participants from 340 contracting companies (trainees include contractors for material contractors, factory services, construction, waste, and other services). After training and evaluation by each facility's EHS departments, 2,384 contractor employees obtained construction permits.

To provide employees with comprehensive health care, USI has built a healthy workplace better than what is required by law. We have on-site nurses and regularly invite specialized family medicine doctors, occupational medicine doctors, psychologists, physiotherapists, and nutritionists to provide employees with psychological, work stress, career, and other consulting services. In 2023, approximately 14,000 health consultations total 9,720 hours. As for amenities, USI nurse stations are equipped with simple wound dressing stations, blood pressure meters, and weighing scales to provide basic healthcare for employees. Nurse stations also have a resting lounge, counseling room, and breastfeeding room for rest, consultations, and breastfeeding. Nantou Facility has received the Nantou County Excellent Breastfeeding Room certification for ten consecutive years, providing a comfortable breastfeeding space for mothers.

Health Risk Management
A healthy workforce is an integral part of a company's competitiveness and a key driver of sustainable growth. To achieve effective health management, USI provides free annual physicals for employees and occupational medical exams for employees in high-risk operating environments, and the results are classified and managed. In addition to complying with laws, regulations, and related guidelines, employees' health risks are analyzed according to the nature of work and the health risk matrix. The top three themes are health management of special health examination management, cerebrovascular and cardiovascular disease prevention and management, and prevention and management of musculoskeletal diseases.
Occupational Health Risk:
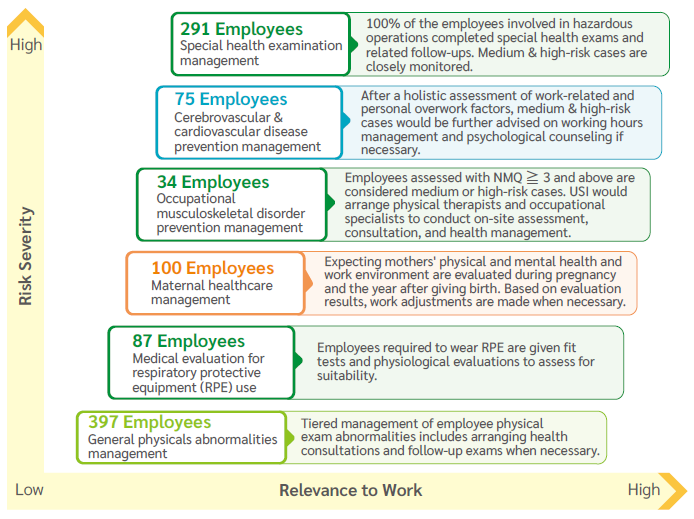
In terms of special health examination management, we analyzed employee health examination results and found no individuals with unusual work-related conditions. Cerebrovascular and cardiovascular disease are closely related to employees' health (physiological) and workload (psychological), while musculoskeletal-related diseases are the first cause of occupational diseases (by industry). Therefore, we set management indicators for metabolic syndrome, cerebrovascular and cardiovascular disease, and musculoskeletal-related disease, as shown in the table below.
Health Risk Issues and Management Metrics:
Issues | Management Metrics | 2023 Performance | Status |
---|---|---|---|
Metabolic Syndrome | Less than 22% | 18.7% | ![]() |
Cerebrovascular and Cardiovascular Disease | Risk level of 3 or more, less than 2% | 0.38% | ![]() |
Musculoskeletal Disorders | NMQ of 3 or more, less than 10% | 2.5% | ![]() |
Health Promotion
Health promotion is an integral part of preventive healthcare. Based on the results of the health examination and the willingness to participate in health promotion activities, USI holds various health seminars, trainings, and activities such as pregnancy healthcare, cancer screening services, vaccination services, blood donation activities, weight-loss competitions, quit smoking contests, and bone density detection to prevent chronic and occupational diseases. USI also encourages employees to exercise regularly, eat and drink healthily, and maintain good living habits.
Annual Health Promotion Activities:
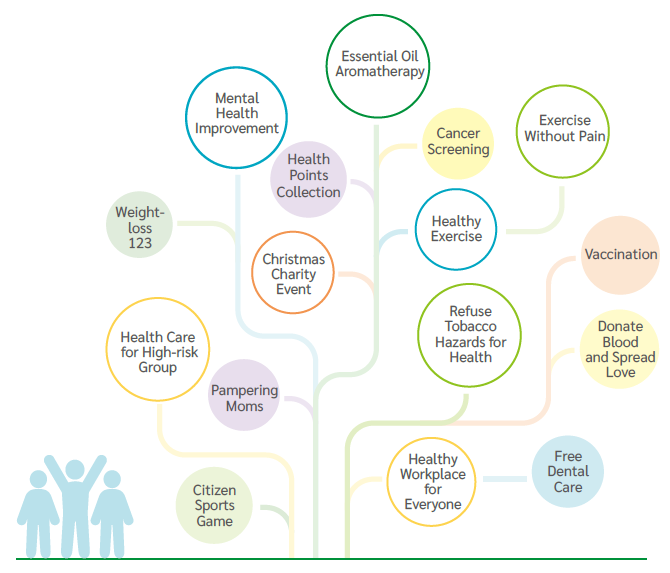
Diverse Health Activities Performance:

- A total of 40 health activities were organized for the whole year, with 10,705 participants and an activity satisfaction above 95%.
- The Nantou Facility was awarded the Healthy Workplace Certification - Health Promotion Label by the National Health Agency.
- More than 4,000 employees attended health promotion activities.
- 1,372 participants took part in the ergonomic hazard prevention program.
- 309 employees participated in tobacco control and prevention activities.